Modular Prefabricated Construction: a circular asset management system for closed-loop supply and logistics chains
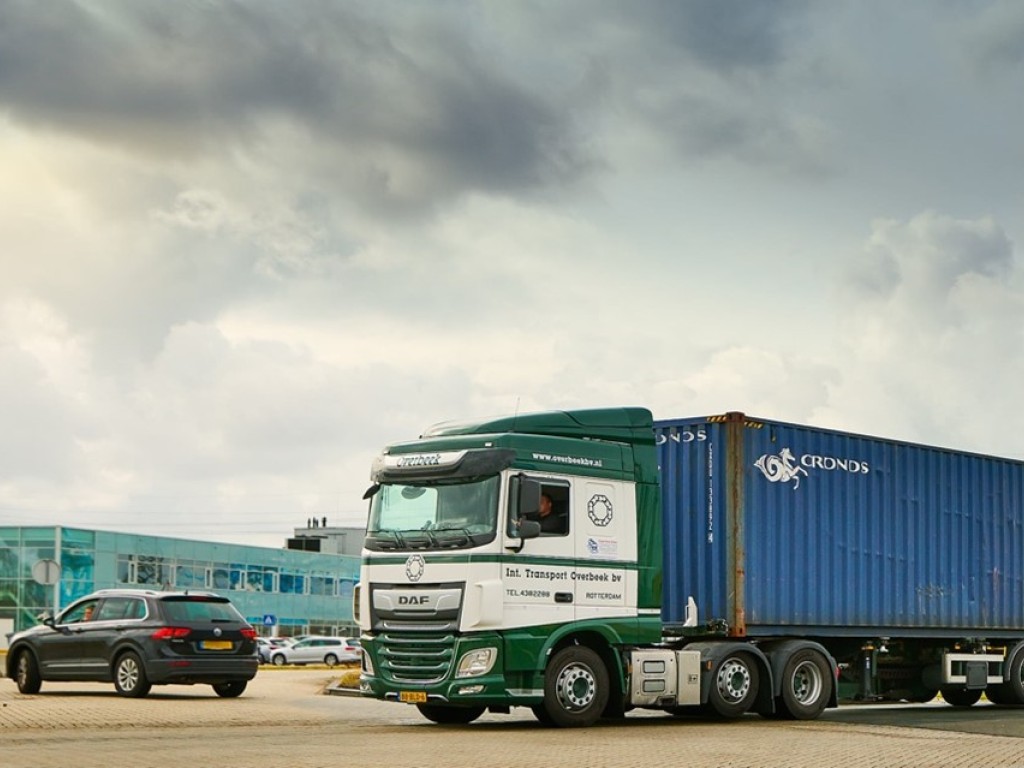
The EU and the Dutch government have set the ambitious goal of a fully circular economy by 2050. In the race towards this target, the Top Sector Logistics set the following targets for the construction industry to be achieved by 2030: (a) 0,4 Mton CO2 reduction, (b) 60% reduction in Nitrogen emissions, (c)75% health gain. To accelerate the achievement of these targets, we have formed a consortium of key academic and industry stakeholders in the construction supply chain. This consortium, formed by Eindhoven University of Technology (TU/e), European Supply Chain Forum (ESCF), De Meeuw, Baetsen, Equans, Van den Broek, TiQiT, ABB and Van Gelder (with the support of the council of Haarlem), will conduct research on the two themes set in the TKI Dinalog call: “Sustainable logistics”, and “Data-driven logistics and chain management”. We will focus on the use of prefabricated modular concepts which are an important enabler for circularity in the construction sector. Modularity enables the construction of adaptable and reversible structures which adapt to changing demand. However, the modular construction sector does not currently exploit its full potential for circularity and a truly closed-loop construction process. This is due to the highly fragmented supply chain and the lack of transparent and efficient data sharing infrastructures which results in poorly coordinated value chain processes where opportunities are missed to reduce footprint emissions thanks to optimized offsite logistics operation and reuse of modules and component to further reduce waste. This research project is aimed at closing the above mentioned gaps, thus accelerating the transition to a digitally integrated closed-loop supply chain for modular prefabricated construction supported by a circular asset management system (CAMS). The work is articulated in five work packages (WPs) and will result in three main deliverables: (1) a roadmap for the transition from the current linear value chain, to the “to-be” closed-loop value chain for modular construction (WP1); (2) a prototype digital twin of the value chain processes especially scoped down to the offsite logistics planning (WP2); (3) a prototype of a distributed peer-to-peer information system for digital product flow (Digital Product Platform – DPP) (WP3). The roadmap will set a clear line of sight for syndicates of stakeholders on the steps for transitioning to a digitally integrated and highly coordinated closed-loop supply chain, with emphasis on the integrative mechanisms to create added value for the entire process. The digital twin will enable scenario analysis for decision-making to develop coordinated production, offsite logistics and onsite assembly/disassembly planning which include the return and reuse of modules. It simulates and assesses the system performance in terms of measurable KPIs directly related to economic value (costs and profit) and CO2 and NOx emissions. The information system will enable data sharing across the key stakeholders in the supply chain for digital product flow, and its architecture will be such that it can be hosted at a large number of locations yet maintaining peer-to-peer connectivity. Field validation of the individual deliverables will be performed in WP4 based on two Living Labs and related use cases, one provided by De Meeuw and one by Van Gelder and the council of Haarlem; for both living labs, the last validation phase will consist of a single combined validation experiment to evaluate how the digital twin and the information system can function in conjunction to support offsite logistics planning. Lastly, WP5 will cover valorization and dissemination towards industry for market activation, and towards the wider scientific community to share scientifically innovative results. Market activation will be pursued via two workshops organized with the support of ESCF and targeted to the wider market professionals to stimulate uptake by industry. The prototypes of the digital twin and information system will be made open source and TU/e will engage actively with interested companies to build on our prototypes and integrate them with their own tools following feasible development plans. Such integrated digital tools, especially for offsite logistics operations in construction, are currently lacking both in the scientific literature and in practice, where available tools cover mainly the design and actual construction activities. With optimized value chain and offsite logistics processes, we expect our results to lead to 85% reduction of CO2 and NOx emissions in relation to construction traffic with modular construction, with respect to a traditional construction setting. The integrated planning of production/logistics/assembly/disassembly will lead to less and more efficient use of equipment onsite, with consequent reduction of CO2 and NOx emissions.